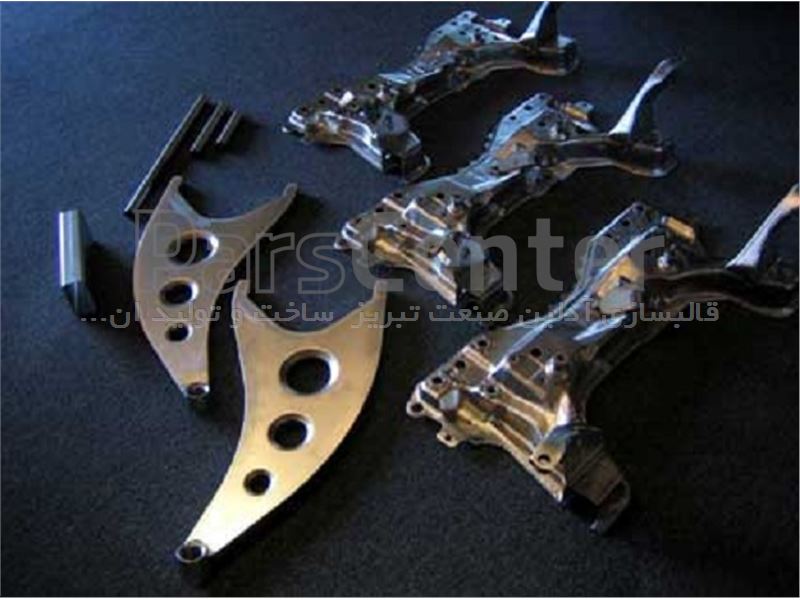
Mold springs, a crucial component in various industrial applications, play a pivotal role in ensuring the efficient functioning of machinery and tools. These unassuming, coiled springs may not receive much attention, but they are the unsung heroes that keep many processes running smoothly. In this article, we will delve into the fascinating world of سنبه برش springs, examining their significance, unique properties, and diverse applications.
Mold springs are specialized coil springs designed to withstand extreme pressure and return to their original shape after being compressed or extended. They are typically made from high-quality materials like steel or stainless steel, which provide them with exceptional strength and durability. This resilience makes them ideal for use in injection molds, where they help maintain the mold’s shape and ensure precise production of plastic or metal parts.
One of the standout features of mold springs is their ability to endure repeated cycles of compression and extension without experiencing significant wear and tear. This remarkable durability not only prolongs their lifespan but also contributes to cost savings by reducing the need for frequent replacements. Moreover, mold springs can withstand the harsh conditions found in many industrial settings, including high temperatures, corrosive environments, and heavy loads.
Another crucial aspect of mold springs is their versatility. They come in various shapes and sizes, allowing them to be customized to meet the specific requirements of different applications. Whether you are working in automotive manufacturing, aerospace engineering, or consumer goods production, mold springs can be tailored to suit your needs. This adaptability makes them an essential component in a wide range of industries.
In injection molding, mold springs are instrumental in maintaining the integrity of the mold cavity. They exert constant pressure on the mold halves, ensuring that they remain securely closed during the injection process. This pressure prevents any potential leaks or deformations in the final product, resulting in higher-quality parts with precise dimensions.